Occupational Hygiene Measurements
Every year in the Kenya, over one million people experience ill health caused or worsened by their working conditions. Several workers per year die from occupational exposure to harmful substances and working days are lost due to work related ill health or injury.
Noise at Work
Action and Protection From Noise at Work
The Noise Regulations requires operators to eliminate or reduce risks to health and safety from noise at work.
Depending on the level of risk, you should:
Take action to reduce the noise exposure
Provide your employees with personal hearing protection
Other duties under the Regulations include the need to:
Make sure the legal limits on noise exposure are not exceeded
Maintain and ensure the use of equipment you provide to control noise risks
Provide your employees with information, instruction and training
Carry out health surveillance (monitor workers’ hearing ability
Daily Personal Noise Exposure (LEP,d)
The Noise Regulations apply where work activities expose people at work (your employees or other workers affected by your work activities) to risks to their health and safety from noise.
Operators are required to make a reliable, representative estimate of your workers’ daily personal noise exposure. Daily personal noise exposure, or LEP,d, represents a daily noise ‘dose’ – a combination of ‘how loud’ and ‘how long exposed’ for the various sources that a person is exposed to in a working day, together with the peak sound pressure levels, LCpeak, to which workers are exposed.
This involves taking measurements in the workplace by “a trained and competent person” to assess the risk to hearing of employees whose work is liable to expose them to noise at, or above, a lower exposure action level, and to determine their exposure.
Measured With Expertise and Accuracy
Lab Works EA use the latest calibrated noise meters, able to measure third octaves, to accurately measure noise at fixed points within the installation, or areas where operators would typically work. Dosimeters, can continuously monitor an individual’s exposure to noise, and provide an assessment of their actual daily personal exposure.
The technical report provided will identify areas for noise control, suitable hearing protection, if necessary, and a noise control plan.
Vibration at Work
Reducing Exposure, Reducing Harm
Workers who are regularly exposed to hand arm vibration may suffer from symptoms due to pathological effects on the peripheral vascular system, peripheral nervous system, muscles and other tissues of the hand and arm. The symptoms are collectively known as hand-arm vibration syndrome (HAVS).
Whole Body Vibration (WBV) can be transmitted to workers through the seat or feet of mobile machines, work vehicles or vibrating surfaces. This can cause a range health risks including back pain
Vibration at work tests, sometimes referred to as Hand Arm and Whole Body Vibration assessments, are carried out in accordance with DOSH Act, which specifies “exposure action values” and “exposure limit values”. They require employers to reduce exposure to harmful levels of vibration to a minimum.
Lab Works EA occupational hygienists possess the appropriate qualifications from the DOSH and have experience across a wide range of industries in Kenya and East Africa conducting hand arm (HAV) and whole body vibration (WBV) testing.
We strongly identify with your commercial needs and offer rapid response times while pro-actively keeping you informed at every stage of the food testing process, In the unlikely event that your product is challenged, we can call upon our network of specialists to provide you with expert support.
Lab Works has a laboratory to provide a range of on-site occupational hygiene services throughout the country including hand arm vibration monitoring and assessments.
Our Services Include:
Measurement and assessment of hand-arm vibration using human-vibration meters and tri-axial accelerometers
Measurement and assessment of whole body vibration
Calculation of maximum permitted daily usage
Consultancy and advice on control strategies
Problem solving
Interpretation of regulations and procedures
Hand – Arm Vibration
Hand-Arm Vibration (HAV) is a major cause of occupational ill health and it is estimated around five million workers are exposed to HAV in the workplace. Two million of these workers are exposed to levels of vibration where there are clear risks of developing disease. Workers whose hands are regularly exposed to high vibration may suffer from several kinds of injury to the hands and arm, which can include: Vascular disorders, generally known as ‘vibration induced white finger’ which cause impaired blood circulation, blanching of affected fingers and parts of the hand Neurological and muscular damage leading to numbness and tingling in the fingers and hands, reducing grip strength and dexterity, and reduced sensitivity both of touch and to temperature. Other possible (less understood) kinds of damage leading to pain and stiffness in the hands and joints of the wrists, elbows and shoulders Collectively the injuries are known as ‘hand-arm vibration syndrome’ (HAVS), which is a painful disease and is widespread in those industries where vibratory tools and machines are used.
Whole Body Vibration
Whole body vibration is shaking or jolting of the human body through a supporting surface (usually the seat or the floor), for example when driving or riding on a vehicle along an unmade road, operating earth moving machines or forklift trucks, or driving rail vehicles or machinery. Lower back problems arise from degeneration in the spinal vertebra or degeneration of the discs causing compression and pain. The lower back muscles can also become weakened, increasing the risk of injury through twisting or manual handling. Each year, approximately new claims for Industrial Injury Disability Benefit are made in relation to vibration white finger and vibration related carpal tunnel syndrome.
Legal Requirements
An exposure limit value is the maximum permitted exposure to vibration for an individual worker. The DOSH Regulations require employers to:
Reduce exposure to harmful levels of vibration to a minimum
Assess the vibration risk to employees
Provide information and training to those exposed
Implement measures to reduce exposure
Provide health surveillance when action levels are reached in order to ensure exposure is below the exposure limit value
Other Occupational Hygiene Services
Lab Works EA’s occupational hygiene expertise is not limited to human vibration monitoring.
Other services include:
Measurement and assessment of exposure to hazardous substances (dusts, fumes, solvents)
Local Exhaust Ventilation (LEV) performance and assessment
Noise surveys, exposure assessment, dosimetry and control
Radiation monitoring
Workplace comfort conditions.
Thermal Assessments
Protecting Workers From the Extremes of Temperature
The thermal parameters of a working environment can vary greatly and the risks to human health can be significant and in extreme instances life threatening.
In hot environments such as foundries and glass making there can be a risk of personnel developing heat stress or heat strain unless strict control procedures are followed. Risks also exist if there is the need to wear personal protective equipment for prolonged periods whilst in hot environments such as chemical manufacturing or asbestos removal.
In cold environments, such as cold storage, or outdoor working during winter periods can cause significant health problems including frostbite and hypothermia.
Lab Works EA have qualified occupational hygienists who can assist in undertaking thermal assessments through the measurement of a range of parameters, including air temperature, mean radiant temperature, humidity, air movement, metabolic work rate and clothing.
The readings are taken and put into appropriate assessment tools (thermal indices) that look at the allowable working times in given conditions and the need to introduce controls to protect workers.
Please refer to the current schedule/scope of accreditation for the current list of accredited tests/matrices, for the specific location. The scope/schedule is available from the relevant laboratory, or may be downloaded from the relevant Accreditation Body website.
Workplace Environment
Evaluating and solving your workplace health issues
Workplace issues can have significant impacts on workers’ health, regardless of the business or industry in which they work. Typically, such issues include:
A. Indoor Air Quality
As the built environment becomes more enclosed and more complex the number of incidents associated with ill-health and discomfort within the workplace have increased.
B. Exposure Monitoring to Minimise Risk
Operator exposure monitoring, sometimes referred to as workplace air monitoring, is undertaken in order to establish the level of hazardous substances workers are exposed to within the workplace.
Operator exposure monitoring requirements are usually determined following risk assessments carried out under the DOSH Regulations 2007.
Monitoring is a further requirement under the DOSH regulations under the following conditions:
If a failure of a control measure could cause ill health
A substance has a workplace exposure limit (WEL) or an in house limit
A check that a control measure used to protect worker’s exposure
Lab Works EA’s has a highly experienced team of qualified occupational hygienists who can assist in producing workplace air monitoring strategies.
Operating exposure monitoring is undertaken in accordance with the most appropriate Methods of Determining Hazardous Substances (MDHS) or by internationally recognised standards or methods published by organisations such as NIOSH, BS EN ISO, OSHA.
Monitoring results are presented in interpretive technical reports compared to WELs and give practical advice to provide control measures where necessary.
Lab Works EA has extensive experience of working within indoor environments, measuring a wide range of parameters which may cause health issues. Our experts ensure minimal disruption to our customers’ operations and are always undertaken with sensitivity and discretion.
C. Lighting
Inadequate or poorly design lighting can cause immediate safety issues but also results in health problems, such as eye strain and headaches.
Technical reports compare lighting levels with guidelines and recommend actions to improve the lighting situation where necessary.
D. Thermal Comfort
Issues with moderate thermal comfort in the working environment are largely subjective but can lead to problems with productivity and morale.
Lab Works EA has experienced occupational hygienists who can measure and assess the thermal conditions in your workplace to determine the level of comfort.
E. Workplace Design
Poor workplace design can cause a range of difficulties for workers, including manual handling injuries, repetitive strain injuries, upper limb disorders and back/neck problems from poor posture.
Lab Works EA have occupational hygiene specialists who are able to carry out a number of ergonomic based assessments on work tasks and working stations relating to manual handling, Display Screen Equipment (DSE) and ergonomics.
Technical assessment reports are provided along with practical advice on appropriate remedial measures.
Air Quality Monitoring & Assessment
Noise & Vibration
Environmental Health & Safety Measurements
Food
Agriculture
Asbestos
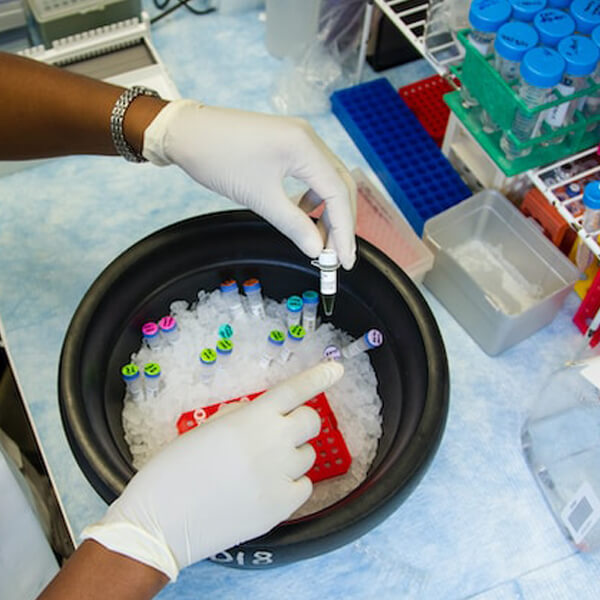
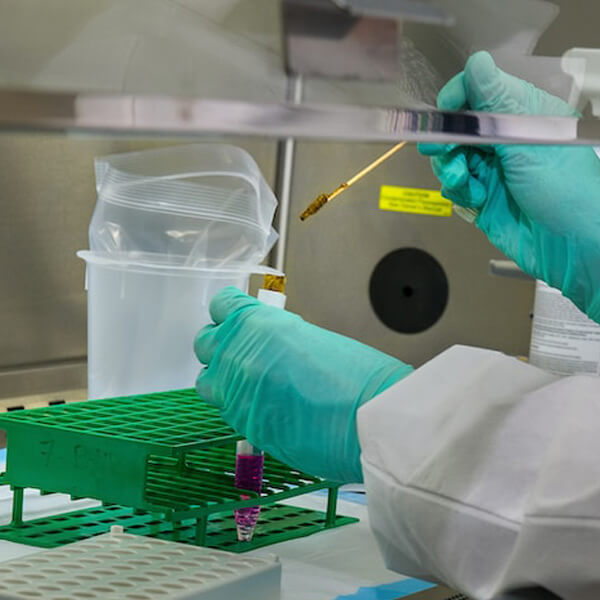
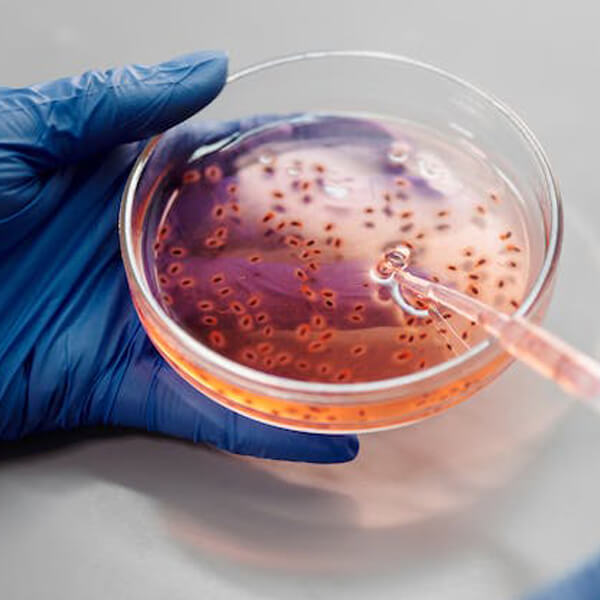
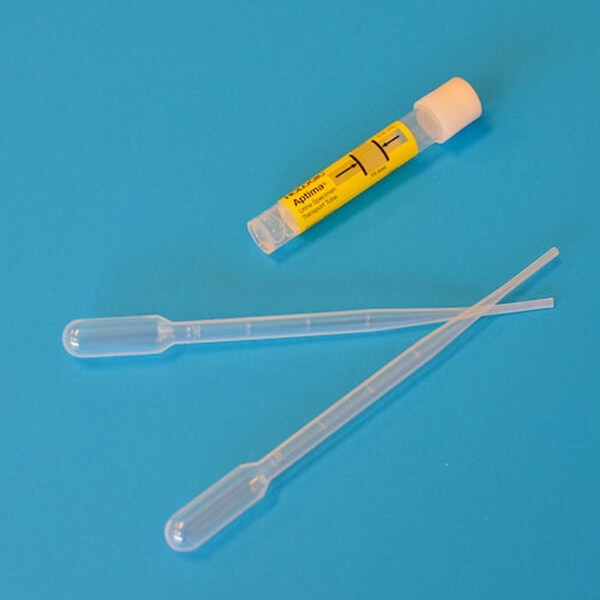